智能制造的概念有些宽泛,对于西门子来说,涵盖了从“工业3.0”到“工业4.0”很长的战线。尽管与其他行业相比,汽车行业在数字化转型道路上走得更远,但就目前发展情况来看,仍有很多问题尚需解决。首先,汽车行业必须转换思维方式,从关注“更佳组合”转向全面掌控整个流程链,同时还要考虑工厂的生命周期。只有这样才能释放出工厂尚未挖掘的潜力。此外,我们还需要理清,在海量的现有数据中哪些是我们需要的,应该在何时何地使用它们,以及如何让这些数据被调用。第三项挑战是系统有序地执行各项标准,因为标准是数字化的基础。
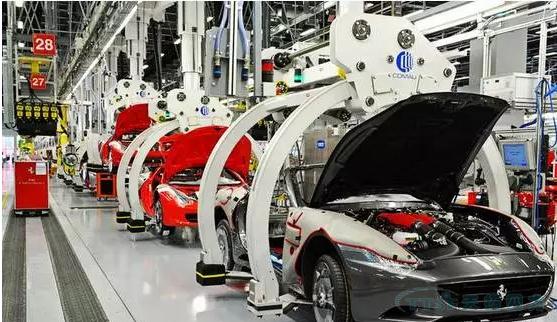
西门子认为数字化企业是通向“工业4.0”和智能制造的必由之路,这一策略需要持续在管理层和员工层普及和培训,并在财务上予以支持,让应用工具和企业数字化水平同步发展。我们可以从以下六个方面考虑。
管理流程
国内车企均尚未制定数字化和自动化总体策略和路径,上汽通用、华晨宝马、广汽丰田这样比较先进的合资厂也只是处于起步阶段,还没有完善的策略和路径。合资企业有部分实际的投资金额,本土车企包括新能源车企都还没有相关投资。所有车企均处于“价值链上各自独立的数据库应用”状态,无法实现贯穿全价值链的企业级数据协作平台。各自独立的数据库造成了新的信息孤岛。产业升级离不开全员素质的提高,特别是管理者的思维认知需要超前一步。大数据方面,多数企业都有各种数据库,但是应用方面还很薄弱,部分合资企业如上汽通用、华晨宝马已经开始企业大数据的分析工作,上汽通用对CRM数据进行分析,华晨宝马则已经着手实施大型数据中心的基础架构建设。
产品设计
越来越多的车企已经从仿制为主转向了自主正向研发,即便是借助国外设计机构。全三维设计已经是国内车企的标配,而要做到多工艺协同对数字化设计软件的要求更高。产品仿真测试的应用已经比较普遍了。产品生命周期管理的系统化使用是车企间比较清晰的分水岭。在产品设计阶段进行制造工艺文档的生成和管理,不仅提高设计工作的系统性,也为后面生产制造环节实现闭环控制提供了可能性。3D打印技术不仅使用在概念车型的制作上,将来也会大量应用在零配件的制造上。合资车企中优秀的企业已经在做虚拟现实技术的尝试,如上汽通用已经聘请专门的虚拟现实设计工程师。
生产规划
在实际产品生产出来之前,一条虚拟的生产线可以帮助工厂进行仿真和优化。“数字化双胞胎”概念就好像真实世界在虚拟世界的镜像,它可以从产品设计阶段一直贯穿到运营服务阶段,使得我们在每一阶段的工作都能达到事半功倍的效果。国内车企的BOM(Bill of Material,物料清单)系统还处于起步阶段,目前只有上汽自主品牌的车型产品数据和BOM已实现在企业全局的BOM系统中管理。三维的产线布置和平衡不仅在投产的时候才有用,在之后的优化、调产、改造阶段能够节省大量的资源。在生产规划软件中嵌入变更的追踪和分析可以使得数据的一致性和效率大大提高。通过对冲压机和机器人系统的仿真,可以在制造单机与生产线之前模拟出实物,缩短生产工期,避免不必要的返工。总装车间的自动化水平较低,信息化水平滞后,因而大部分车企难以在总装车间实现虚拟仿真、虚拟装配与人机工程学,一汽和上汽通用也只能部分实现。在四大工艺日趋成熟的今天,要填补动力总成的研发和质量这块短板,测试系统不可或缺。
工程实施
一系列自动化创新应用会让企业节省大量工作,而统一的标准化的软硬件和通讯,让工程数据保持高度一致的同时,并在水平和垂直方向上的集成,进而使企业在已有的“工业3.0”基础上又一次腾飞。控制器、分布式 I/O、人机界面(HMI)、传动、运动控制系统、电机管理系统等都可以无缝集成到一个单一的工程环境。目前只有上汽大众和华晨宝马等少数企业能够贯彻这样的标准化。企业管理水平要提高,统一的标准化文件必不可少。如果将机械设计的过程与电气数据联系到一起,就可以自动生成PLC程序和相应的E-CAD布局方案。这是工程实施阶段跨越性的一步。大部分车企还难以实现自动化设备配置和程序的自动生成,基本处于人工编程调试的阶段。虚拟调试是自动化技术的革命性突破,在虚拟世界和真实世界之间搭起了桥梁,国内已经有少数先行企业掌握了这项技术。车企车间内以太网一统天下,如果通讯规约统一,会让通讯组态和调试变得更加简单和迅捷。大数据依赖于底层数据的收集,打通垂直数据集成通道是“工业4.0”的重要标志。就目前国内所有车企的企业IT架构现状,均难以实现垂直数据通道从底层自动化感知层直达企业管理层。
制造执行
基本的制造管理系统已经成为汽车生产线中不可缺少的一部分,用于收集生产线上有关设备和质量管理的信息。但是使用的实际效用可以说差距很大。精益制造体系的生产执行系统在合资车厂中已经基本贯彻,本土车厂也在逐步推行这种理念。公司作业过程中文件传递电子化的趋势比较明显。全自动化的物流设备和系统已经在少数车企实现,下一步是与供应商的物流系统对接的时刻。“工业4.0”的理想状态是每时每刻都能够追踪产品加工状态,产品会告诉机器设备,它已经经过几道工序,现在应该实施哪种工艺。在制造执行阶段,系统性地进行物流仿真和产能分析属于高阶技能。得此技能者得天下。要实现按需生产,ERP电子系统必须和消费者/渠道连接在一起。实现这一点还有很长的路要走。
维护服务
汽车制造商想要维持长期的竞争优势,更大化工厂的生产可靠性和设备综合效率,同时优化总体拥有成本是关键的成功因素。将无意义的大数据“big data”变身成为智慧数据“smart data”,才能利用这些数据制定更加明智的决策。不管是新建厂还是老厂,都可以建立三维的工厂模型,这是下一步透明工厂的基础。透明工厂意味着实时可用的全厂数据流可以在比如说云端用来生成真实工厂的虚拟镜像工厂,管理者可以随时调看工厂状况。戴上VR或者AR眼镜,整个工厂就可以呈现在面前。
实施问题管理系统,不仅要求有经验的专家解决问题,重要的是要有预案和完善的机制,使得每次问题的出现都能让我们找到漏洞和缺陷,让企业运营和管理更上一层楼。
维护服务外包的情况在未来劳动力减少、知识密度提高的趋势下会越来越多。一些企业已经实施了能源监控方案,但是还不知道如何利用已经收集的数据。定期维护固然重要,然而预防性维护在提高工厂可靠性上能够贡献更多。对工厂里成千上万的传感器产生的大数据进行挖掘,必然能找出很多可以进一步优化和改造的机会,这也就是所谓的大数据驱动的服务。在这一点上,数据云的应用和发展已经成为看得见的未来。
有关工业信息安全的考虑,合资车企更为完善,本土车企在这方面的意识比较弱,或者说怀着未知的恐慌,而这在未来工业智能制造框架内占据了重要的位置。