一、CNC数控机床数据采集现状
CNC数控机床作为制造业的核心设备,其运行状态和加工过程的数据对于生产监控、设备健康管理和性能优化至关重要。传统的数据采集方法往往依赖于人工巡检或定期维护,存在数据滞后、效率低下等问题。而现代CNC设备通常具备丰富的数据接口和通信协议,如发那科(Fanuc)的Focas2、西门子的OPC-UA等,为数据采集提供了便利条件。随着工业4.0时代的到来,物联网技术在制造业中的应用愈发广泛,特别是在数控机床(CNC)领域,其高效、智能的特点正引领着制造业的转型升级。边缘计算网关作为连接边缘设备与云端的桥梁,在CNC数控机床数据采集中发挥着关键作用。
边缘计算网关部署在网络的边缘侧,即靠近数据源的地方。它主要负责在边缘设备和云服务器之间进行数据传输和处理,实现数据的实时响应和高效处理。边缘计算网关可以作为边缘设备的代理,将数据传输到云端进行集中处理,同时也可将云端的计算结果反馈回边缘设备,实现双向通信。
边缘计算网关的工作原理主要包括数据采集、数据处理和数据传输三个环节:
数据采集:通过传感器等设备采集边缘设备(如CNC数控机床)产生的数据,并进行预处理和清洗,确保数据的准确性和可靠性。
数据处理:根据设定的策略和算法对数据进行本地计算和分析,将部分计算结果返回给边缘设备,减少对云端的计算需求,提高响应速度。
数据传输:将经过处理的数据通过安全可靠的通信协议传输到云端服务器,为后续的云端计算和数据分析提供支持。
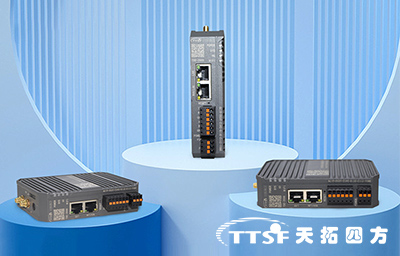
二、边缘计算网关在CNC数控机床数据采集中的应用
实时数据采集与传输
边缘计算网关能够实时采集CNC数控机床的运行状态、加工过程等数据,并通过5G、WiFi等无线网络技术将数据传输到云端。这种实时数据采集与传输机制,使得生产管理人员能够随时了解机床的运行情况,及时作出调整和优化,提高生产效率和产品质量。
故障预警与诊断
通过对CNC数控机床运行数据的实时分析,边缘计算网关能够发现潜在的故障隐患,并及时向生产管理人员发送警报信息。这种故障预警机制能够显著降低生产故障的发生率,提高生产过程的稳定性和连续性。同时,边缘计算网关还能提供故障诊断功能,帮助技术人员快速定位故障原因,减少维修时间和成本。
工艺参数优化
边缘计算网关通过对CNC数控机床加工过程的数据分析,可以深入了解每个工序的运行情况及其对产品质量的影响。基于这些数据,生产管理人员可以调整工艺参数,使生产过程更加精确和高效。这不仅可以减少生产过程中的误差和废品率,还可以提高产品的一致性和可靠性。
跨平台与灵活性
许多CNC设备支持跨平台的TCP协议,这使得边缘计算网关在数据采集过程中具有更高的灵活性和兼容性。无论CNC机床采用何种操作系统或通信协议,边缘计算网关都能通过相应的接口实现数据的实时采集和传输。
三、应用案例
以某机床生产企业为例,该企业引入了边缘计算网关,将传统的CNC数控机床升级为智能机床。智能机床通过内置的传感器采集运行数据,如温度、振动、转速等,并通过边缘计算网关实时传输到云端。云端服务器对数据进行集中处理和分析,为生产管理人员提供实时的监控和决策支持。通过这一系统,该企业实现了生产过程的智能化管理,显著提高了生产效率和产品质量。
边缘计算网关在CNC数控机床数据采集中的应用,为制造业的智能化转型提供了强有力的技术支持。通过实时数据采集与传输、故障预警与诊断、工艺参数优化等功能,边缘计算网关能够显著提升生产过程的稳定性和效率,降低生产成本,提高产品质量。随着工业4.0的深入推进,边缘计算网关将在更多领域发挥重要作用,推动制造业向更加智能、高效的方向发展。
