在飞机制造领域,核心零部件的质量直接关系到飞行安全与性能。近年来,随着工业物联网技术的快速发展,飞机核心零部件生产制造企业通过引入集团IoT平台并对关键数据进行采集与分析,显著提升了良品率和一次合格率,实现了生产质量的优化与突破。
一、客户介绍
某知名飞机零部件制造企业,其生产流程涵盖精密加工、材料检测及装配等复杂工序。在传统生产模式下,产品质量检测主要依赖人工操作与经验判断,不仅效率低下,还极易出现差错。
为解决这一问题,该企业引入了基于天拓四方集团IoT平台的智能制造平台,将生产设备、传感器和数据分析系统深度整合,实现了生产全流程的数字化管理。
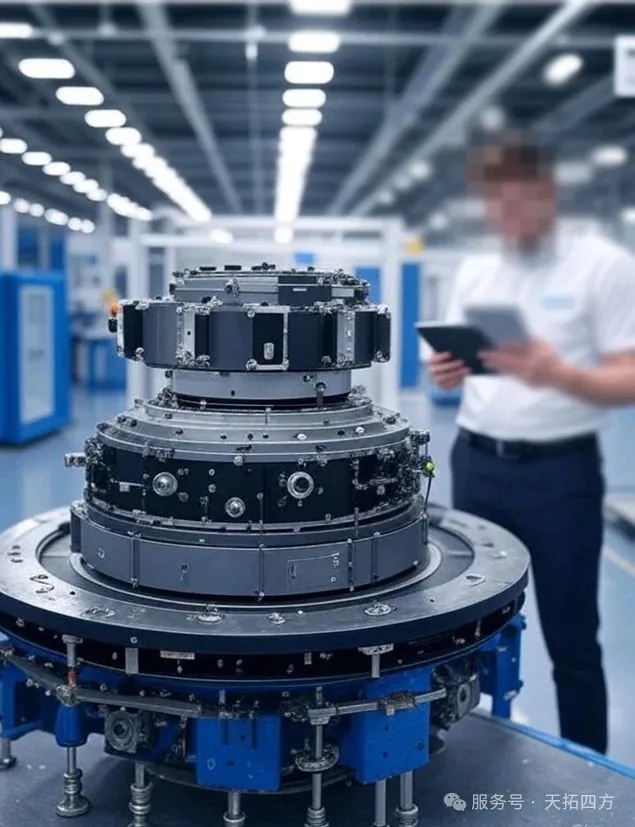
二、天拓四方集团IoT平台解决方案
基于天拓四方集团IoT平台,该企业首先对生产设备的关键运行参数进行实时采集。
例如,加工中心的主轴转速、刀具磨损状态、切削温度等数据通过传感器实时传输至云端。同时,原材料的性能参数、加工过程中的环境变量(如温度、湿度)也被纳入数据采集范围。这些数据通过高速网络汇集到中央控制系统,形成统一的数据池,为后续分析提供了基础。
在数据分析方面,企业采用了高效的数据分析和处理技术,对采集到的海量数据进行处理。通过对历史数据的建模分析,系统能够识别出影响产品质量的关键因素。
例如,在某关键零部件的加工过程中,数据分析发现刀具磨损程度与加工精度之间的强相关性。基于这一发现,企业优化了刀具更换周期,并在加工参数上进行微调,有效降低了因刀具磨损导致的次品率。
此外,通过集团IoT平台还实现了异常检测功能,当设备运行参数偏离正常范围时,系统会自动报警并暂停生产,避免了潜在的质量问题。
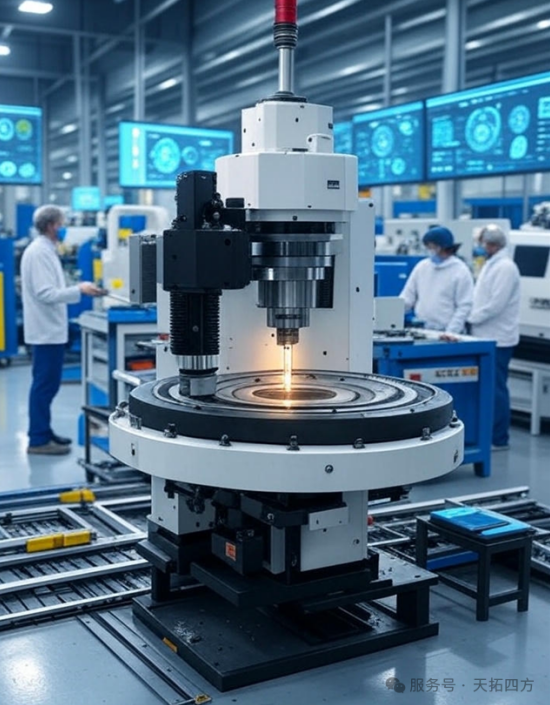
三、客户收益
在本次项目中,集团IoT平台的实施显著提升了企业的质量指标,良品率从原来的95%提升至99%,一次合格率从97%提高到98%。这一变化也得益于对生产过程的精细化管理,在热处理工序中,基于平台通过实时监控炉内温度和冷却速度,确保了每批叶片的材料性能一致性,减少了因工艺波动导致的缺陷。此外,平台还支持了质量追溯功能,一旦发现问题产品,可迅速定位到具体批次和生产环节,大幅降低了排查成本。
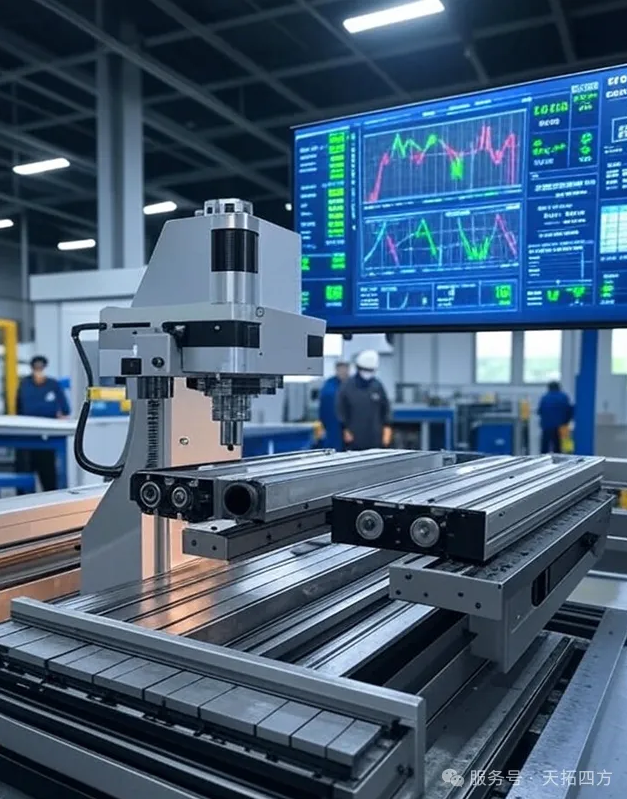